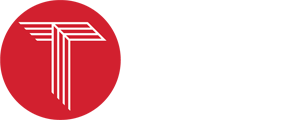
Gruenberg Industrial Oven Options
Gruenberg takes pride in building flexible standard equipment that can be readily modified to better suit specific customer applications. Choose from the following variety of standard options to customize your Gruenberg oven. We offer various controllers and recorders, interior and exterior modifications, make-up air filtration, heating and cooling options, and solvent venting and explosion-resistant packages for your oven. Don’t see what you need, just ask.
Note: Some of the options shown are standard on some ovens. Be sure to check the individual specification sheet for the type of oven you want.
Monitoring and Controlling Industrial Oven Operations
CONTROLLERS
- PROGRAMMABLE TEMPERATURE CONTROLLER: MULTI-SEGMENT The Partlow 1462 optional programmable controller with digital set, digital readout, and thermocouple sensor can function as a normal process control or execute any of eight setpoint profiles. Each profile can have six ramp and six soak segments. Any number of profiles can be linked together. Accuracy: ±0.25% of scale range.
RECORDERS
- SINGLE AND DOUBLE PEN RECORDERS
- Honeywell 4300 GP Solid-state, electronic recorder, in single or double pen, is available with either 24-hour or 7-day recording and has a 10" diameter circular chart. The recorder system comes with a thermocouple temperature sensor accurate to within .5% of range scale.
- Partlow ARC 4100 Single or double pen recorder is available with either 24-hour or 7-day recording and has a 10" diameter circular chart. The recorder system comes with a type J thermocouple.
- STRIP CHART RECORDER You can document your processes with unprecedented precision and accuracy with multiple channels and multiple inputs with this high speed, Eurotherm Chessell microprocessor-based recorder. Three different chart forms can be printed: trend, tabular, or deviation.
- OTHER RECORDERS A variety of recorders are available to meet your specific needs. Please consult your Gruenberg representative for availability.
DOOR LOCKS AND SWITCHES:
- Automatic Door Locks If your product requires uninterrupted processing, these optional pneumatic or electric door locks will provide additional safety so that the interior environment will not be accidentally disturbed when the oven is in process. This option is not available on conveyor ovens.
- Door Switch To save energy, especially when you load and unload your oven frequently, the optional door switch turns off the heaters and circulation system when the door opens. This option is not available on conveyor ovens.
TIMERS
- 24-HOUR CLOCK Used to start or stop the oven any hour of the day or night, complete with skip-a-day feature. Large ovens have a bypass switch with pilot light to indicate automatic mode.
- 24-HOUR CLOCK WITH COOLDOWN THERMOSTAT Same as above with cool-down thermostat.
- PROCESS TIMER Automatic reset timers are wired to start when operating temperature is first attained. You may specify 1 hour, 2.5 hours, 10 hours, 30 hours, or 60 hour settings. The timer will shut off power to heat but the blower will continue to run.
- END-OF-CYCLE THERMOSTAT WITH TIMER Recommended for high temperature ovens above 650° F, the timer will shut down at the end of the cycle. The blower will continue to run until the oven reaches the lower preset point: below 200° F for safety.
- TIMER BELL Bell will sound at the end of the cycle.
- OTHER TIMERS Gruenberg offers a wide variety of optional timers, from a simple heat shutoff to a dual timer.
ELECTRICAL
- MAIN POWER DISCONNECT SWITCH For safe electrical maintenance of the unit, a main power disconnect switch can be installed on the access door of the control box. This necessitates the power to be disconnected before allowing the panel to be opened. Disconnects can be fused or non-fused and a circuit breaker may be specified too.
- SCR POWER CONTROL The Chromalox control minimizes temperature swings at the setpoint by proportioning power to the heaters thus avoiding heat surges and providing excellent uniformity throughout the oven chamber as well as energy savings.
- ALTERNATE VOLTAGES 230V, 1Ø and 3Ø, 60 Hz. are standard. Alternate voltages include:
- 208V
- 380V, 3Ø
- 440, 460, 480, 3Ø
- 550V, 3Ø
- 50 Hz.
Industrial Oven Exterior Options
DOORS
- VERTICAL LIFT DOORS These space saving doors
help to simplify loading. An overhead clearance must be present.
Counterweights assist in all three methods:
- Manual lift
- Electric motor lift
- Pneumatic lift
- HORIZONTAL SLIDE-BY DOORS These doors save space and simplify loading. Three methods available:
- Manual slide
- Electric motor slide
- Pneumatic slide This option is not available on conveyorovens.
- PASS THROUGH DESIGN This design is used for pass through applications where doors are placed on both the front and the back of the oven. Standard 2'' port with threaded cap 15.6 ft3 650° F bench oven with optional stand and optional viewing window
- ELECTRIC DOOR INTERLOCKS Prevents both doors of a pass through design to be opened simultaneously.
- VIEWING WINDOW Allows you to view your work in progress without disrupting the oven environment. A triple-pane 10" x 10" viewing window is standard. Other custom sizes are available upon request. Not available on ovens over 1000° F.
- SUPPORT STAND A welded structural angle stand with a heat-resistant paint provides a convenient working height. Optional adjustable leg levelers are available. Enclosed or cabinet-type stands are also available. This option is not available for Truck-in ovens.
- PORTS Standard port design consists of a 2" sleeved tube through the oven wall with a thermal isolation ring to eliminate heat passage to the shell; includes rubber plug or threaded cap. Other sizes are available.
Industrial Oven Interior Options
- STAINLESS STEEL INTERIOR Stainless steel is offered in place of our usual aluminized-steel liners on ovens below 1000°F. All ovens, 1000°F and above have stainless steel interiors as a standard.
- SHELVING Additional shelving is available in perforated stainless steel, or solid angle-framed stainless steel. Any custom shelving designs can be accommodated as well. This option is not available for conveyor ovens.
- CONTINUOUSLY-WELDED LINERS A continuously-welded liner may be specified to separate the process environment from the insulation and prevent contamination. Continuously welded liners are commonly used with specific atmospheres such as nitrogen or CO2, humidity, or flammables. Note: Continuously Welded liners must be stainless steel.
- LIGHT Optional interior light is recessed into an internal
box and controlled by an exterior switch mounted on the control panel.
Optional interior lighting is not available on ovens above 1000° F.
Industrial Oven Filtration of Make-up Air
- HEPA FILTERS Optional American Air HEPA filters can be installed on the air intake or circulation plenum. The filters are 99.99% efficient at particles 0.3 microns or larger and are effective up to 500°F.
- INLET AIR FILTERS Available in stainless steel, coated aluminum mesh, or fiberglass, these filters keep dirt and dust out of the oven environment. Filters are cleanable and replaceable.
FORCED COOLING
- AMBIENT AIR COOLING Optional forced air cooling provides quick economical cool down of product for rapid unloading. An automatic damper is furnished that opens when forced cooling is engaged.
- MECHANICAL REFRIGERATION COOLING A mechanical refrigeration
package can be supplied for forced-cooling with either a single or
cascade system depending upon your requirements.
CO2 COOLING SYSTEM High reliability and rapid cooling are the reasons for liquid CO2 cooling. The system includes an indicating temperature control, solenoid valve, line strainer, selection switch, pilot lights, and connection base. Stainless steel interiors and continuously-welded liners are recommended with this system.
ALTERNATE HEATING
- DIRECT FIRED GAS SYSTEM The electric system will be replaced by an Eclipse gas system with all of the necessary piping, valves, and regulator. This option is not available on Bench and Laboratory ovens.
- INDIRECT FIRED GAS SYSTEM A tube firing gas burner is fitted to the oven and fired into a stainless steel schedule 10 heat exchanger. A gas regulator is supplied with the Eclipse gas system. This option is not available on Bench or Laboratory Ovens.
- STEAM HEATING SYSTEM Steam Heating is accomplished by means of a copper-tube steam coil with extended aluminum surface fins. This option is not available on Bench or Conveyor ovens.
Special Processing Requirements
- NITROGEN PURGE The nitrogen purge system creates a nitrogen atmosphere within the work chamber. An automatic high and low flow apparatus includes two inlet valves and a purge timer. The high flow quickly fills the work chamber and the low flow then maintains the resulting nitrogen levels. A continuously welded liner, a water-cooled seal at the circulation fan shaft, and a double door gasket are needed with this system. This option is not available on conveyor ovens.
- EXHAUST BLOWER Optional exhaust blower removes fumes from the oven chamber at a rate that is set based on the loading characteristics. Note: additional wattage may be needed due to heat loss encountered when using a powered exhaust.
Solvent Venting Class A Industrial Ovens
All standard Gruenberg ovens can be designed to house volatile atmospheres. Gruenberg designs all Class A ovens to conform to OSHA, NFPA 86A, Factory Mutual (FM), and Factory Insurance Association (FIA) requirements.
NOTE: The exterior of these ovens is not designed to operate within a volatile atmosphere. Ovens which perform this function are known as Explosion Resistant Ovens.
As part of the safety design, Class A ovens must be equipped with a high exhaust rate: since the heating elements are an ignition source, a high exhaust rate is needed to dilute the volatile vapors below the “lower explosive limits.” As a result, the heating elements’ KW must be sufficiently increased to compensate for the heat loss caused by the above-normal exhaust rate. In addition, for a Class A oven to be energy efficient, the additional KW required must be carefully calculated according to solvent load and operating temperature requirements as demonstrated on the following page.
The following “safe oven design” requirements are set by OSHA and NFPA 86A for Solvent Venting Class A ovens.
- Explosion venting: pressure relief latches (already standard on most Gruenberg cabinet and truck-in ovens) or separate caged or hinged explosion relief panels.
- A separate powered exhauster sized according to solvent load and operating temperature.
- Heating systems interlocked by differential switches with both the exhaust and circulation systems so that loss of airflow automatically shuts down the heat.
- A purge timer to effect a minimum of four complete changes of the oven air volume before the heater is energized.
- A fail safe, separate, manual reset, High Limit thermostat to shut down the heat if there is a primary control failure (standard on all Gruenberg Ovens).
- Electric ovens require a second heater contactor to be associated with the High Limit thermostat on electric ovens (standard on all Gruenberg Ovens).
- A Door switch to shut down power to the heater and circulation fan/blower if the oven door is open during operation.
- Markings on the oven including various warning labels and a capacity curve showing maximum solvent load at a given temperature.
- In addition, gas ovens must have an automatic electric ignition with pilot flame supervision by an electronic device; a main gas safety valve; high and low gas pressure switches; and a differential switch should a mixer be used.
- Port for fire extinguisher system (optional, but recommended).
USING THE CHART: The scale across the bottom of the chart can be used for pints and gallons. The curves represent maximum solvent load for a particular blower over a range of temperature. Each curve is labeled and color coded: black for gallons; red for pints. Note: this chart is for rough estimates only. Do not mount on oven for reference.
VENTILATION FOR SOLVENT LOADS
Calculating the exhaust rate is very important in a Class A Oven. It must be high enough to be safe, but it should not be so high that it’s wasteful. Solvent loads must be realistically calculated to conserve energy.
FM (Factory Mutual Association) and FIA (Factory Insurance Association) set the standards for ventilation rates. Both FM and FIA require that in temperatures below 250°F, 530 CFM per gallon must be exhausted.
Rough estimates to determine solvent load are both unreliable and unprofitable. Here is an example to illustrate the point: in a 96 ft3 horizontal circulation cabinet oven capable of 450°F, an exhaust rate of 960 CFM is needed to meet ventilation requirements. Therefore, 107 extra KW are required to compensate for the heat loss caused by the high exhaust rate. That is 3 times the normal power, just for ventilation. According to precise calculations however, that includes evaporation and other losses between formulating and loading, the actual measure of solvent might only be a pint. This would require only 140 CFM for ventilation, which means only 16 KW would be needed to compensate for the heat losses; one seventh of the amount calculated for one gallon of solvent. The power saved by proper computation of solvent loads is substantial.
CALCULATING ADDITIONAL KW If you know how much solvent is in your load, you can use the following charts to get a rough idea of the exhaust rate required. Once you have found the proper CFM for your solvent load, you can calculate the additional KW needed to compensate for the exhaust rate. Use the following equation:
Explosion-Resistant Ovens
All standard Gruenberg ovens can be modified to be explosion-resistant. Explosion-resistant ovens incorporate design features that allow the oven to be operated within a volatile atmosphere defined as Class I, Group D or Class II, Group E, F, or G. Specifically, these design features include the following:
- Non-sparking brass explosion-relief door latches
- Fully-welded liners and removable air circulation ducts and baffles (when dusting loads are dried)
- Heating coil sealed within a seamless Incoloy tubular element
- Electrical connections entering the oven through sealed ports and terminating in approved explosionresistant housings.
- Wiring encased in rigid conduit or approved mineral insulated cable
- Non-sparking aluminum or brass blowers or circulation fans
- Approved, static-eliminating belt drives
- Explosion-resistant motors
- Approved, explosion-resistant electrical equipment and controls enclosed in explosion-resistant housing or purged boxes
CODE DEFINITIONS
Class I locations require the type explosion-proof electrical equipment where, in case of an explosion, the hazardous flames would be contained. In Class II or III locations, dust, fibers, and flyings are the combustible materials and it is only necessary to keep these materials out of the electrical equipment (where an arc may take place) and to maintain safe external temperatures. A brief explanation of the three classifications covering Hazardous Locations follows:
- Class I Locations Flammable gases or vapors are or may be present in the air in quantities sufficient to produce explosive or ignitable mixtures.
- Class I, Division I Hazardous concentrations of flammable gases or vapors exist continuously, intermittently, or periodically under normal operating conditions.
- Class I, Division 2 Hazardous concentrations of flammable gases or vapors are handled in closed containers or closed systems.
- Class II Locations The presence of combustible dust present a fire or explosion hazard.
- Class II, Division I Dust is suspended in the air continuously, intermittently or periodically under normal operating conditions, in quantities sufficient to produce explosive or ignitable mixtures.
- Class II, Division 2 Dust is not suspended in the air, but where deposits of it accumulating on the electrical equipment will interfere with the safe dissipation of heat, causing a fire hazard.
- Class III Locations Easily ignitable fibers or flyings are
present but not likely to be suspended in the air in quantities
sufficient to product ignitable mixtures.
- Class III, Division I Ignitable fibers or materials producing combustible flyings are handled, manufactured, or used.
- Class III, Division 2 Easily ignited fibers are stored or handled (except in process of manufacture). Further refinement created for the purpose of testing and approving electrical equipment divides Class I into four separate designations, A, B, C, D and Class II into three separate designations, E, F, and G. Underwriters’ Laboratories test and approve electrical equipment for the following specific groups:
- Class I, Group A Atmospheres containing acetylene.
- Class I, Group B Atmospheres containing hydrogen, or gases or vapors of equivalent hazard such as manufactured gas.
- Class I, Group C Atmospheres containing ethyl-ether vapors, ethylene, or cyclo-propane.
- Class I, Group D Atmospheres containing gasoline, hexane, naphtha, benzene, butane, propane, alcohol, acetone, benzyl, lacquer solvent vapors, or natural gas.
- Class II, Group E Atmospheres containing metal dust, including aluminum, magnesium, and their commercial alloys, and other metals of similarly hazardous characteristics.
- Class II, Group F Atmospheres containing carbon black, coal or coke dust.
- Class II, Group G Atmospheres containing flour, starch or grain dusts.